La produzione industriale si basa su una serie di elementi fondamentali che garantiscono il buon funzionamento degli impianti e dei macchinari.
Tra questi, i componenti meccanici svolgono un ruolo cruciale: sono gli ingranaggi, i giunti, le staffe, i supporti, e molte altre parti indispensabili che consentono di trasformare l’energia in movimento e di realizzare prodotti in modo efficiente. Quando si parla di componenti meccanici, spesso ci si riferisce a pezzi standardizzati, prodotti in serie e compatibili con la maggior parte delle macchine. Tuttavia, in molti casi, le soluzioni standard non soddisfano appieno le esigenze specifiche di un’azienda.
Ecco perché la progettazione e realizzazione di componenti meccanici su misura sta diventando sempre più importante: adattare le parti meccaniche alle necessità peculiari di un impianto o di un prodotto consente di raggiungere livelli di prestazione, qualità ed efficienza che altrimenti sarebbero difficilmente ottenibili.
Perché Scegliere Componenti Meccanici Su Misura
Personalizzazione e Specificità del Progetto
Ogni settore industriale ha le sue esigenze peculiari. Una soluzione di serie rischia di essere troppo generica e non perfettamente compatibile con i requisiti di una determinata applicazione. Progettare un componente su misura significa ottimizzarne dimensioni, forma e funzionalità in base al contesto operativo. Ad esempio, in un macchinario destinato a lavorare in ambienti altamente corrosivi, sarà fondamentale scegliere materiali resistenti alla corrosione. In un altro caso, potrebbe essere essenziale ridurre al minimo l’attrito interno per garantire un funzionamento più fluido.
Aumento dell’Efficienza Produttiva
Un componente correttamente dimensionato e realizzato ad hoc migliora l’efficienza produttiva. Si riducono i malfunzionamenti, diminuiscono gli interventi di manutenzione straordinaria e si abbassano i costi di fermo macchina. In molti impianti industriali, un semplice arresto può generare costi elevatissimi a causa delle interruzioni nella catena di produzione: riuscire a prevenire tali inconvenienti grazie a componenti meccanici ottimizzati significa risparmiare tempo e denaro.
Miglioramento della Qualità del Prodotto Finale
Un macchinario che opera in modo più preciso e stabile produce, nella maggior parte dei casi, pezzi o prodotti di qualità superiore. L’utilizzo di componenti su misura riduce le tolleranze di errore e aumenta la ripetibilità del processo. In settori come l’automotive o l’aerospaziale, dove la precisione è fondamentale, i componenti su misura diventano spesso una scelta obbligata per mantenere standard qualitativi elevati.
Competitività e Innovazione
Il mondo industriale è in continua evoluzione, con soluzioni sempre più avanzate e macchinari dalle prestazioni elevate. Utilizzare componenti meccanici personalizzati permette di innovare più rapidamente, sperimentare nuove soluzioni ingegneristiche e differenziarsi dalla concorrenza. Un’azienda che investe nell’ottimizzazione dei propri processi produttivi e offre un prodotto migliore ottiene un vantaggio competitivo di rilievo.
I Principali Passi nella Progettazione di Componenti Meccanici Su Misura
1. Analisi delle Esigenze
La prima fase prevede un confronto approfondito tra il cliente e l’azienda di progettazione e produzione. Si raccolgono i dati relativi alle condizioni d’uso del componente (temperature, carichi, ambiente operativo, cicli di lavoro), alle prestazioni richieste (velocità, precisione, resistenza a particolari sollecitazioni) e al budget disponibile. Questa fase è fondamentale per definire i requisiti di progetto e le specifiche funzionali.
2. Studio di Fattibilità e Proposta di Soluzioni
Sulla base delle informazioni raccolte, i progettisti effettuano uno studio di fattibilità tecnica e presentano le possibili soluzioni che soddisfano i requisiti. Questa fase può includere la revisione di componenti esistenti, l’analisi di eventuali criticità e la proposta di alternative in termini di materiali o processi produttivi. Gli strumenti utilizzati in questa fase possono comprendere software di calcolo e simulazione (CAD, FEM – Finite Element Method) per verificare la resistenza strutturale, l’eventuale deformazione, le vibrazioni e l’usura.
3. Progettazione Dettagliata e Modellazione CAD
Dopo aver concordato la soluzione migliore, si passa alla progettazione dettagliata tramite software CAD (Computer-Aided Design). Questa fase comprende:
- Disegni tecnici: definizione delle quote, delle tolleranze, delle finiture superficiali e di ogni aspetto geometrico del componente.
- Simulazioni aggiuntive: eventuali test di stress termico o meccanico, simulazioni di flusso se il componente è esposto a fluidi o gas, analisi delle sollecitazioni dinamiche.
- Ottimizzazione: sulla base dei risultati delle simulazioni, si interviene per ridurre pesi superflui, modificare la geometria al fine di migliorare la rigidità o la resistenza, e rendere la parte più facile da produrre.
4. Prototipazione e Test
Una volta completata la progettazione, spesso si realizza un prototipo per verificare concretamente le caratteristiche del componente. In questa fase, possono entrare in gioco diverse tecniche:
- Stampa 3D (Additive Manufacturing): ideale per prototipi rapidi e per valutare la geometria prima di passare a processi più complessi.
- Lavorazioni in piccola serie: tornitura, fresatura o trattamenti superficiali su alcuni pezzi per validare la soluzione in condizioni reali.
Gli eventuali test funzionali (stress test, prove in camera climatica, controlli dimensionali) consentono di apportare modifiche prima di avviare la produzione in serie.
5. Produzione e Controllo Qualità
Dopo la validazione del prototipo, si passa alla produzione vera e propria. I processi utilizzati variano in base al componente e ai materiali scelti. Può trattarsi di fresatura, tornitura, rettifica, trattamenti termici, saldatura, stampaggio o un mix di queste tecnologie. Una parte cruciale di questa fase è il controllo qualità, che deve garantire la rispondenza del prodotto ai disegni tecnici. Tra le procedure di controllo più comuni ci sono:
- Controlli dimensionali con calibri, micrometri o macchine di misura a coordinate (CMM).
- Controlli non distruttivi (NDT) come radiografie, ultrasuoni o liquidi penetranti per rilevare difetti interni o superficiali.
- Test prestazionali (ad esempio, test di coppia o sforzo) per assicurarsi che il componente operi secondo le specifiche richieste.
Tecnologie di Produzione: Tra Tradizione e Innovazione
Lavorazioni Meccaniche Tradizionali
Le lavorazioni tradizionali come fresatura, tornitura, foratura e rettifica restano al centro della produzione di componenti su misura. Macchinari a controllo numerico (CNC) consentono di ottenere tolleranze molto ristrette, ridurre errori umani e assicurare una ripetibilità elevata.
- Fresatura CNC: perfetta per lavorare superfici complesse e creare geometrie tridimensionali con grande precisione.
- Tornitura CNC: ideale per parti di forma cilindrica o coniche, anche in grandi serie.
- Rettifica: utilizzata quando è necessario ottenere un’elevata finitura superficiale e tolleranze minime, come nel settore aeronautico.
Additive Manufacturing (Stampa 3D)
La stampa 3D sta rivoluzionando il mondo della produzione, offrendo la possibilità di realizzare componenti con geometrie molto complesse. Per quanto riguarda i metalli, tecnologie come la Direct Metal Laser Sintering (DMLS) o la Selective Laser Melting (SLM) stanno aprendo nuove frontiere, permettendo di produrre parti con proprietà meccaniche molto buone e con un risparmio di materiale significativo. Il vantaggio dell’additive manufacturing è la libertà di design: si possono creare strutture interne ottimizzate dal punto di vista del peso, canali di raffreddamento integrati e forme impossibili da ottenere con i metodi convenzionali.
Trattamenti Superficiali e Termici
Un aspetto fondamentale nella realizzazione di componenti su misura è la scelta del trattamento superficiale o termico più adeguato. Questi trattamenti permettono di migliorare la resistenza all’usura, la durezza, la resistenza a corrosione o l’estetica della parte. Alcuni esempi:
- Tempra e Rinvenimento: processi termici che incrementano la durezza e la resistenza del metallo.
- Rivestimenti superficiali: come la nichelatura, la cromatura dura o i rivestimenti PVD (Physical Vapor Deposition).
- Zincatura: molto comune nei componenti destinati ad ambienti soggetti a corrosione (umidità, agenti chimici).
Scelta dei Materiali: Metalli, Polimeri e Compositi
Acciai e Leghe Metalliche
L’acciaio è sicuramente il materiale più utilizzato nell’industria meccanica, grazie alla sua versatilità e resistenza. Esistono numerose varianti (acciai al carbonio, acciai inossidabili, leghe speciali) ognuna con proprietà specifiche. Anche l’alluminio è un materiale molto diffuso, apprezzato per la sua leggerezza e buona lavorabilità. In settori ad alte prestazioni, come l’aerospaziale, si fa largo uso di leghe di titanio, leggere e resistenti ma più costose e difficili da lavorare.
Polimeri Tecnici
I polimeri tecnici (come il PEEK, il poliuretano, il PTFE) trovano impiego quando è necessaria una buona resistenza chimica, un basso coefficiente di attrito o un peso ridotto. Inoltre, i polimeri possono essere lavorati con macchine CNC, ma spesso la produzione in serie avviene tramite stampaggio a iniezione.
Materiali Compositi
I materiali compositi, come la fibra di carbonio o la fibra di vetro, vengono impiegati soprattutto nei settori che richiedono un elevato rapporto resistenza/peso (ad esempio nello sport, nelle corse automobilistiche o nell’aeronautica). La progettazione di un componente in materiale composito richiede competenze specifiche, poiché bisogna considerare non solo la forma del pezzo, ma anche l’orientamento delle fibre e i processi di stratificazione.
Integrazione con la Manutenzione Predittiva e l’Industria 4.0
L’adozione di componenti meccanici su misura non si limita alla semplice produzione. Oggi, con lo sviluppo dell’Industria 4.0, la digitalizzazione dei processi e l’Internet of Things (IoT), è possibile dotare i macchinari di sensori che monitorano costantemente lo stato di salute dei vari componenti. Un componente meccanico personalizzato può essere progettato per integrare sensori di temperatura, vibrazione o pressione, fornendo dati in tempo reale. Questo favorisce la manutenzione predittiva, riduce al minimo i fermi macchina inaspettati e ottimizza ulteriormente i costi operativi.
Settori di Applicazione
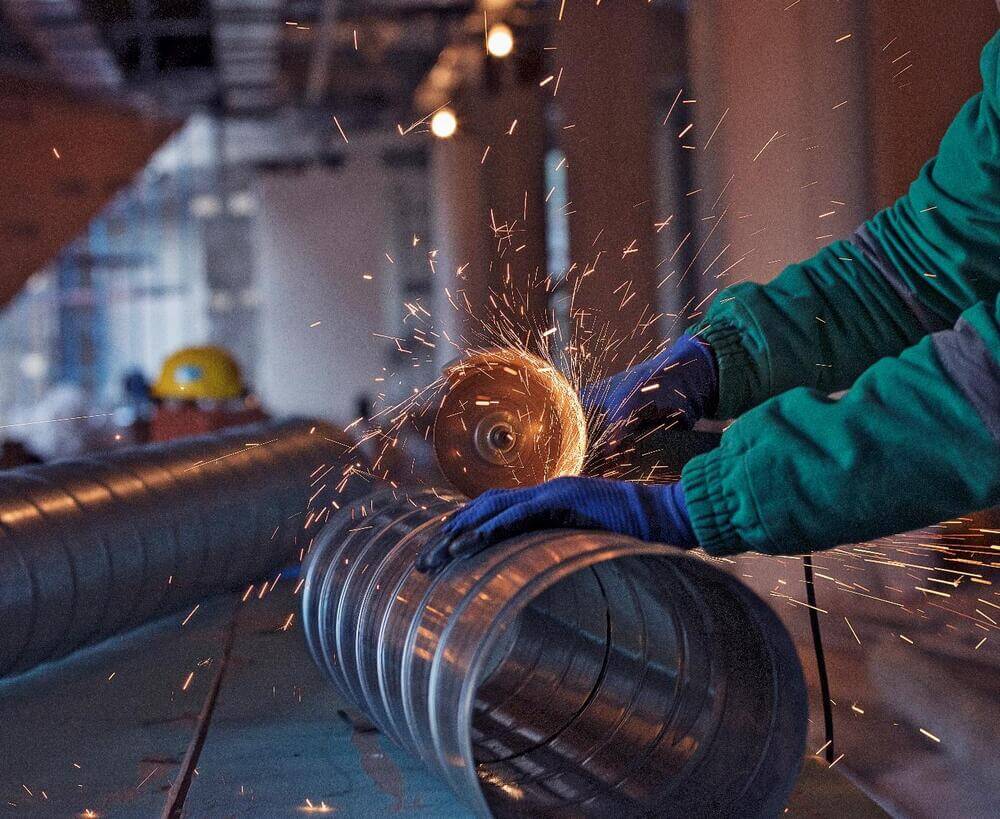
Automotive e Motorsport
Nel settore automobilistico, la ricerca delle massime prestazioni e la riduzione del peso rendono indispensabile l’uso di componenti su misura. Nei motori ad alte prestazioni, gli alberi a camme, i pistoni o i collettori di scarico possono essere progettati e realizzati specificamente per un determinato modello. Nel mondo del motorsport, ogni grammo conta e ogni componente deve essere ottimizzato al dettaglio per raggiungere prestazioni eccellenti.
Aerospaziale
Qui la precisione è tutto: un piccolo errore di tolleranza può determinare un guasto catastrofico. I componenti devono essere leggeri ma estremamente resistenti a vibrazioni, stress termico e pressioni estreme. L’uso di materiali avanzati come leghe di titanio o compositi in fibra di carbonio è molto diffuso.
Alimentare e Farmaceutico
Nel settore alimentare e farmaceutico, oltre alla precisione e all’efficienza, contano moltissimo la sicurezza e l’igiene. Le superfici dei componenti devono essere facili da pulire e resistenti a prodotti chimici di detergenza aggressivi. Acciai inox di alta qualità e trattamenti superficiali specifici sono la norma in questi settori.
Macchine Utensili e Automazione
Le linee di produzione automatizzate necessitano di componenti in grado di funzionare a ritmi elevati, spesso con movimenti ripetitivi. Affidabilità e durata sono fondamentali per ridurre i tempi di fermo macchina. Qui i componenti su misura si rivelano decisivi per garantire un’integrazione perfetta con gli altri sistemi di automazione (robot, sensori, sistemi di visione).
Considerazioni Economiche: Costo Vs. Investimento
Progettare e realizzare un componente su misura può sembrare più costoso rispetto all’acquisto di un pezzo standard. Tuttavia, è importante analizzare il costo totale di possesso (TCO, Total Cost of Ownership). Un pezzo standard, anche se inizialmente più economico, potrebbe creare problemi di compatibilità, dover essere sostituito più spesso o causare inefficienze produttive. Al contrario, un componente personalizzato permette di:
- Ridurre i tempi di fermo e i costi di manutenzione.
- Migliorare la qualità del prodotto e la produttività complessiva.
- Evitare spese future per adattamenti o modifiche.
In questo senso, l’investimento in un componente su misura si ripaga nel medio-lungo termine, garantendo un ritorno economico significativo.
Come Scegliere il Partner Giusto
Quando si tratta di realizzare componenti meccanici su misura, la scelta del partner produttivo è essenziale. Ecco alcuni fattori da considerare:
- Esperienza e Settori di Riferimento: Verificare che l’azienda abbia esperienza nel proprio settore industriale e conosca le normative e gli standard di qualità richiesti.
- Competenze Tecniche: Un team di ingegneri qualificati, in grado di utilizzare strumenti di simulazione e prototipazione.
- Capacità Produttive e Tecnologiche: La disponibilità di macchinari all’avanguardia (CNC, additive manufacturing, trattamenti termici e superficiali, collaudi) che permettano di coprire internamente tutto il ciclo produttivo.
- Qualità e Certificazioni: È importante che l’azienda sia certificata ISO 9001 (o certificazioni specifiche di settore) e abbia procedure di controllo qualità ben definite.
- Flessibilità e Servizio Post-Vendita: La capacità di fornire supporto anche dopo la consegna, offrendo eventualmente servizi di manutenzione e riparazione rapida, è un segnale di affidabilità.