La fresatura CNC (Computer Numerical Control) è un processo di lavorazione meccanica indispensabile in numerosi settori industriali.
Dall’automotive all’aerospaziale, passando per l’elettronica e la meccanica di precisione, la fresatura CNC consente di ottenere pezzi metallici complessi con tolleranze molto strette e finiture superficiali di alta qualità.
Ma in cosa consiste esattamente questo processo?
Quali sono le fasi principali di lavorazione e quali vantaggi offre rispetto ad altri metodi di produzione? In questo articolo scopriremo tutto ciò che occorre sapere sulla fresatura CNC, con informazioni pratiche, suggerimenti per aumentare la produttività e consigli su come ottenere risultati ottimali.
Cos’è la fresatura CNC
La fresatura è un processo di asportazione di truciolo in cui un utensile rotante (fresa) rimuove progressivamente materiale da un pezzo per dargli la forma desiderata. Quando parliamo di fresatura CNC, ci riferiamo a una tecnologia che utilizza macchine a controllo numerico per automatizzare e controllare con estrema precisione ogni fase del processo.
In particolare, un sistema computerizzato elabora un programma (G-code) contenente le istruzioni di taglio e guida i movimenti dell’utensile e del pezzo, ottenendo lavorazioni di alta accuratezza in maniera ripetibile.
La fresatura CNC è particolarmente diffusa nella lavorazione dei metalli, come acciaio, alluminio, rame e leghe speciali.
Tuttavia, esistono anche numerose applicazioni su materiali plastici, resine e persino legno. Rispetto alla fresatura tradizionale, il vantaggio di affidarsi a un sistema di controllo numerico è la possibilità di realizzare geometrie complesse e di mantenere un elevato livello di coerenza e qualità tra i vari pezzi prodotti.
Principali componenti e funzionamento di una macchina CNC
Per comprendere al meglio il funzionamento della fresatura CNC, è fondamentale conoscere i principali componenti di una macchina di questo tipo. Ecco i più importanti:
- Telaio e struttura portante
Le macchine CNC sono dotate di un telaio robusto, solitamente in ghisa o acciaio, che garantisce la stabilità necessaria per ridurre le vibrazioni durante la lavorazione. Una struttura rigida assicura precisione di posizionamento dell’utensile e contribuisce a preservare la qualità dell’operazione di taglio. - Mandrino
Il mandrino è il componente rotante che tiene in posizione la fresa. Può raggiungere velocità di rotazione molto elevate (dai 3.000 fino ai 50.000 giri al minuto, a seconda del modello e del materiale da lavorare). La scelta del mandrino adeguato incide su precisione, finitura superficiale e tempi di produzione. - Piano di lavoro o tavola
Dove si fissa o si blocca il pezzo da lavorare. Può essere dotato di morsa, staffe o sistemi di fissaggio vacuum. Alcune macchine sono a 3 assi (X, Y, Z), mentre altre possono arrivare a 4, 5 o più assi di movimento, permettendo lavorazioni molto complesse anche su superfici inclinate o curve in modo continuo. - Motori e azionamenti
I motori (stepper o servo) trasformano le istruzioni digitali in movimenti reali sugli assi della macchina, garantendo la posizione e l’avanzamento corretto dell’utensile rispetto al pezzo. Sistemi a ricircolo di sfere, guide lineari e cinghie dentate possono assicurare scorrevolezza e precisione. - Unità di controllo (Controller)
Il cervello della macchina, che elabora il codice di programmazione (G-code) e coordina i movimenti del mandrino e degli assi. Può essere integrata nella macchina stessa o gestita tramite un computer esterno con software specifico. - Sistema di lubrificazione e raffreddamento
Durante la fresatura, l’attrito genera calore. Per preservare l’utensile e il pezzo, è fondamentale utilizzare un sistema di lubrificazione e raffreddamento (ad esempio, emulsioni o oli interi) che riduca l’attrito e favorisca l’evacuazione del truciolo.
Il funzionamento di base prevede che il pezzo sia fissato in modo sicuro sulla tavola della macchina e che l’utensile ruoti ad alta velocità. I movimenti degli assi vengono gestiti dal controller secondo le istruzioni di un file CAM (Computer-Aided Manufacturing), precedentemente generato a partire dal modello CAD (Computer-Aided Design).
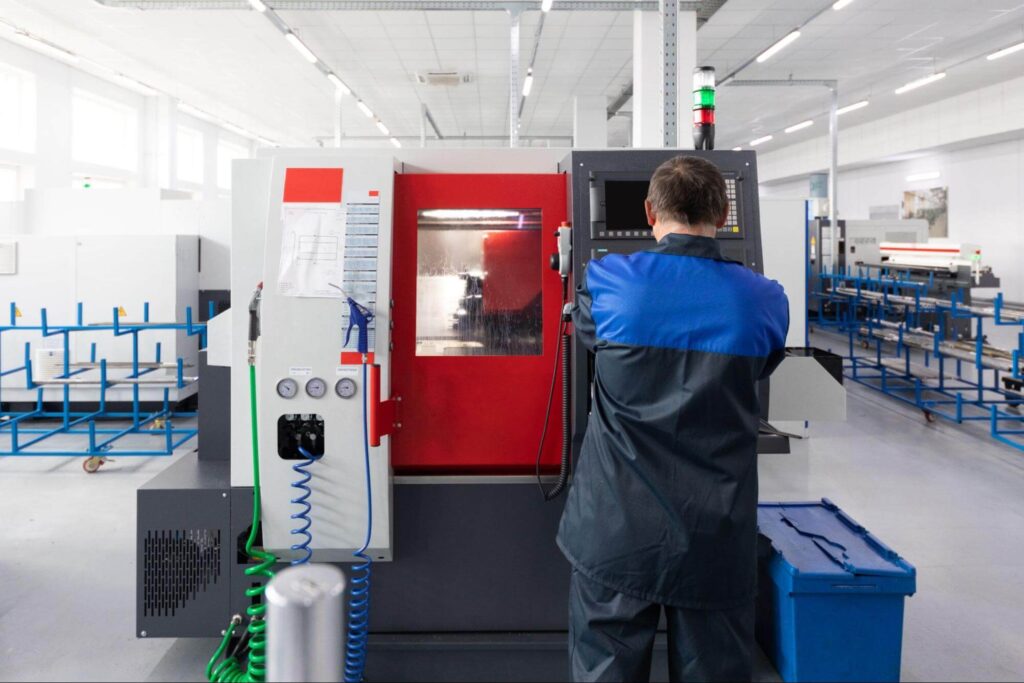
Vantaggi della fresatura CNC
L’adozione di sistemi CNC nella fresatura comporta una serie di benefici, sia in termini di produttività che di qualità del prodotto finito:
- Elevata precisione e ripetibilità
Una volta impostato il programma corretto, la macchina può riprodurre lo stesso pezzo con tolleranze minime (anche dell’ordine di qualche micron, in applicazioni di altissima precisione). Ciò è essenziale in settori dove la conformità dimensionale è di primaria importanza. - Riduzione dei tempi di lavorazione
Il controllo numerico consente di automatizzare processi complessi, riducendo i tempi morti e le operazioni manuali. Il risparmio di tempo si traduce in maggiore produttività e costi operativi ridotti. - Maggiore sicurezza
L’operatore interagisce con la macchina principalmente nella fase di setup (fissaggio del pezzo, installazione dell’utensile) e di controllo finale. Durante la fresatura, la macchina lavora in autonomia, limitando il contatto diretto con utensili a elevata velocità di rotazione e riducendo il rischio di incidenti. - Flessibilità di progettazione
Grazie ai software CAD/CAM e alla programmazione CNC, è possibile realizzare forme complesse senza la necessità di dedicare molto tempo all’attrezzaggio. Ciò rende la fresatura CNC adatta sia a grandi serie sia a produzioni limitate con design personalizzati. - Ottimizzazione dell’uso dei materiali
La precisione del processo permette di ridurre gli sprechi di materiale, poiché si può programmare la traiettoria dell’utensile in modo molto preciso, evitando aree inutilmente asportate o difetti che costringono a scartare il pezzo.
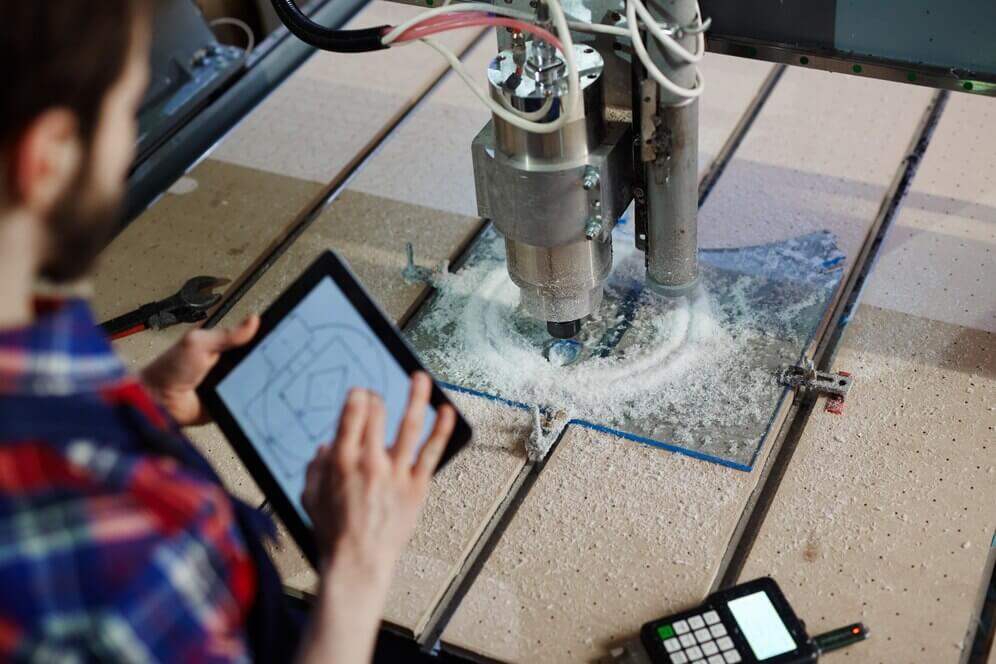
Materiali e strumenti di lavorazione
La fresatura CNC per metalli spazia tra un’ampia gamma di materiali, ognuno con caratteristiche meccaniche specifiche e diverse esigenze di taglio:
- Acciaio dolce, inox e legato: molto comune in settori come l’automotive, l’aerospaziale e la meccanica generale. La lavorazione dell’acciaio richiede frese in carburo e parametri di taglio appropriati per evitare eccessivo calore e usura rapida dell’utensile.
- Alluminio e sue leghe: apprezzato per la leggerezza e l’elevata lavorabilità. Consente velocità di taglio maggiori rispetto all’acciaio, con utensili che favoriscono la rapida evacuazione del truciolo.
- Rame e ottone: metalli duttili, utilizzati in componenti idraulici, impianti elettrici e decorazioni. La fresatura di questi materiali è relativamente agevole ma va tenuta sotto controllo la tendenza all’impastamento dell’utensile.
- Titanio e leghe speciali: molto utilizzati in ambito aerospaziale e medicale. Sono metalli complessi da fresare, poiché producono calore elevato e possono comportare usura accelerata dell’utensile.
Per quanto riguarda gli strumenti, le frese sono tipicamente in:
- HSS (High Speed Steel): utilizzate per lavori su materiali non troppo duri o per prototipazioni meno impegnative in termini di velocità di taglio.
- Carburo (Widia): offrono maggiore durezza e resistenza all’usura, ideali per produzione in serie e lavorazioni impegnative.
- Frese con rivestimenti speciali: ad esempio frese al nitruro di titanio (TiN), nitruro di titanio alluminio (TiAlN) o diamante policristallino (PCD) per lavorazioni su alluminio abrasivo o compositi.
Fasi del processo di fresatura CNC
Per garantire precisione e efficienza, la fresatura CNC segue diverse fasi, ognuna delle quali richiede attenzione ai dettagli e competenze specifiche:
1. Progettazione CAD
Il primo passo consiste nella creazione del modello 3D del pezzo attraverso un software CAD (come SolidWorks, Fusion 360, CATIA o Inventor). In questa fase, si definiscono tutte le caratteristiche geometriche e dimensionali, incluse eventuali forature, tasche, spallamenti e finiture superficiali.
2. Programmazione CAM e generazione G-code
Una volta definito il modello CAD, si passa al software CAM (Computer-Aided Manufacturing) per pianificare le strategie di asportazione del materiale. Qui si impostano parametri quali:
- Tipologia di utensile
- Velocità di taglio (in metri al minuto o giri/min)
- Avanzamento (in mm/min)
- Profondità di passata
- Strategia di fresatura (contornatura, sgrossatura, finitura, ecc.)
Il software genera poi un codice macchina (G-code), in cui ogni riga di istruzione specifica la posizione dell’utensile e i movimenti sugli assi. Questo file viene caricato nel controller CNC.
3. Setup della macchina
Prima di avviare la produzione, l’operatore deve:
- Fissare il pezzo sul piano di lavoro con un sistema di bloccaggio adeguato.
- Montare e azzerare l’utensile (o gli utensili, se si dispone di un magazzino utensili automatico).
- Verificare che i parametri di lubrificazione o di refrigerazione siano correttamente impostati.
Un corretto setup è determinante per evitare errori di misura o difetti di stabilità che possano compromettere la qualità del pezzo.
4. Operazioni di fresatura
In questa fase, la macchina esegue i movimenti prescritti dal G-code, rimuovendo il materiale in eccesso e conferendo al pezzo la forma voluta. L’operatore supervisiona il processo, controllando eventuali anomalie quali:
- Vibrazioni eccessive
- Surriscaldamento dell’utensile o del pezzo
- Usura anomala dell’utensile
- Difetti di superficie o dimensioni fuori tolleranza
Se necessario, è possibile effettuare delle pause per sostituire o raffreddare gli utensili e per monitorare l’avanzamento della lavorazione.
5. Controllo qualità e finitura
Al termine della fase di fresatura, si procede con il controllo dimensionale, utilizzando strumenti di misura come calibri digitali, micrometri, altimetri o macchine di misura a coordinate (CMM). In caso di superfici con finiture di altissima qualità, può essere necessaria un’ulteriore lavorazione di levigatura o lucidatura. Solo dopo aver verificato la conformità del pezzo rispetto alle specifiche di progetto, si dichiara la lavorazione completata.
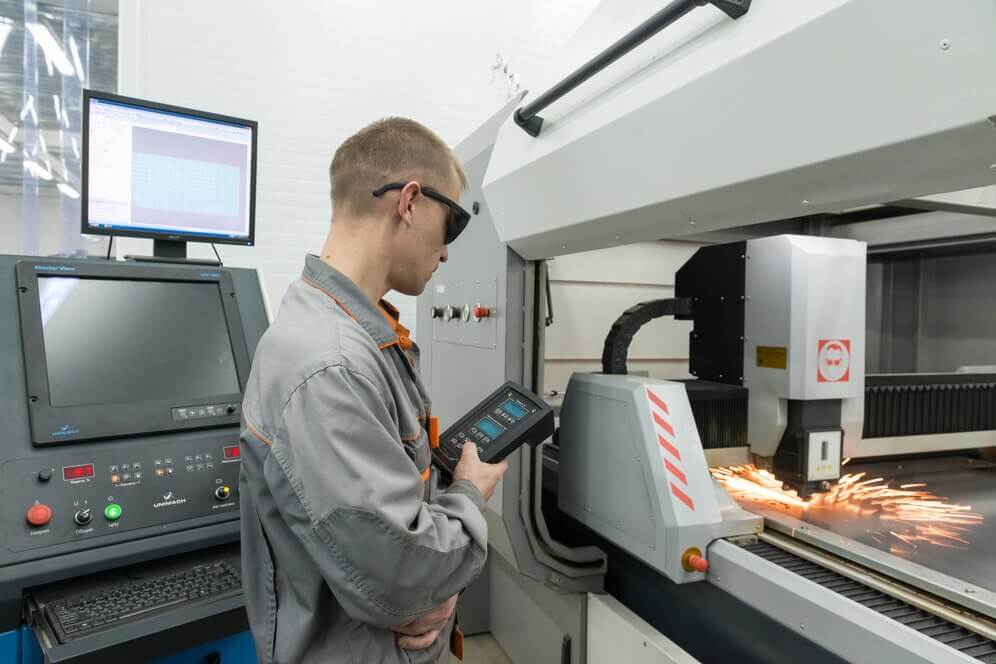
Applicazioni industriali della fresatura CNC
La fresatura CNC ha un campo di applicazione estremamente vasto, grazie alle sue possibilità di personalizzazione e all’elevata precisione ottenibile. Alcuni esempi di settori in cui trova impiego:
- Automotive
Produzione di componenti del motore, scatole del cambio, strutture e supporti per carrozzeria, stampi per parti in plastica. - Aerospaziale
Lavorazione di alluminio, titanio e leghe leggere per realizzare pale di turbine, strutture per ali e fusoliere, componenti di satelliti e razzi. - Medicale
Produzione di protesi, impianti dentali, strumenti chirurgici e attrezzature di laboratorio in materiali biocompatibili. - Elettronica
Creazione di involucri, dissipatori di calore, componenti per schede elettroniche in alluminio o rame. - Meccanica di precisione
Realizzazione di ingranaggi, stampi, modelli, elettrodi di erosione e vari elementi con tolleranze estremamente ridotte. - Settore dell’energia
Pezzi di turbine per centrali elettriche, componenti di impianti eolici, supporti per pannelli solari e molto altro.
Buone pratiche per massimizzare efficienza e precisione
Affinché la fresatura CNC risulti competitiva, è necessario adottare alcune buone pratiche che permettono di ridurre tempi e costi di produzione, garantendo al contempo risultati di alta qualità:
Manutenzione preventiva
- Pulizia e lubrificazione: rimuovere il truciolo accumulato, verificare lo stato degli ugelli e sostituire periodicamente il liquido refrigerante.
- Controllo degli organi di trasmissione: monitorare cinghie, viti a ricircolo di sfere, guide lineari e motori, così da intervenire prima che subiscano usura eccessiva.
- Aggiornamenti software: mantenere il controller e i software CAM sempre aggiornati, così da beneficiare delle ultime funzioni e correzioni di bug.
Ottimizzazione dei parametri di taglio
- Velocità di taglio (Vc): parametro che indica la velocità relativa tra l’utensile e il pezzo, generalmente espresso in metri al minuto (m/min). Una velocità troppo alta può causare surriscaldamento e usura rapida dell’utensile; una velocità troppo bassa aumenta i tempi di lavorazione.
- Avanzamento (F): velocità di traslazione dell’utensile rispetto al pezzo, di solito espressa in mm/min o mm/giro. Un avanzamento corretto garantisce un buon compromesso tra asportazione e finitura.
- Profondità di passata: regola la quantità di materiale asportato in un singolo passaggio. Una profondità troppo elevata può sovraccaricare l’utensile e la macchina, mentre una troppo bassa allunga i tempi di lavorazione.
Scelta degli utensili
- Geometria della fresa: la forma dell’utensile (numero di taglienti, angolo di spoglia, elica, ecc.) influenza direttamente la capacità di rimozione truciolo e la finitura superficiale.
- Materiale dell’utensile: l’uso di frese in metallo duro rivestite permette di sostenere velocità di taglio elevate e mantenere la durata dell’utensile.
- Uso corretto degli inserti: in alcune macchine, gli utensili hanno inserti intercambiabili. Scegliere il giusto inserto consente di lavorare materiali diversi con un unico porta utensile, riducendo i costi di tooling.
Come ridurre errori e difetti di lavorazione
Nonostante l’automazione e il controllo numerico, possono verificarsi difetti o problemi di fresatura. Ecco alcune strategie per prevenirli:
- Verificare la rigidità del sistema
Vibrazioni o giochi meccanici influenzano negativamente la precisione del taglio. Assicurarsi che morsetti e staffaggi siano ben serrati e che la macchina non presenti anomalie o usura. - Mantenere il pezzo in temperatura costante
Alcuni metalli, come l’alluminio, hanno un alto coefficiente di dilatazione termica. Lavorare in un ambiente a temperatura controllata riduce il rischio di errori dimensionali. - Monitorare costantemente l’usura dell’utensile
Un utensile consumato genera finiture scadenti, può creare bave o danneggiare il pezzo. Pianificare cambi utensile periodici previene difetti e garantisce uniformità. - Impostare correttamente i parametri di taglio
Eccesso di calore e truciolo mal evacuato possono portare a bruciature superficiali, deformazioni o rotture improvvise dell’utensile. Seguire le indicazioni fornite dal produttore di utensili e sperimentare con test controllati per raggiungere un equilibrio ottimale. - Effettuare controlli in-process
L’uso di sonde di tastatura o sistemi di misura integrati nella macchina permette di verificare dimensioni e posizioni durante la lavorazione, intervenendo subito in caso di scostamenti rilevanti.
Trend tecnologici e prospettive future
La fresatura CNC non è un campo statico, bensì in continua evoluzione grazie alle innovazioni tecnologiche. Alcuni trend da tenere d’occhio:
- Automazione avanzata e Industria 4.0: integrazione di sensori IoT, analisi dei dati in tempo reale e sistemi di monitoraggio a distanza per ridurre fermi macchina e ottimizzare la produzione.
- Stampa 3D ibrida: alcune macchine combinano additivi e sottrattivi (fresatura), permettendo di costruire una parte in additive manufacturing e rifinirla poi con frese CNC, offrendo possibilità di design altrimenti irrealizzabili.
- Software sempre più evoluti: i pacchetti CAM di ultima generazione forniscono simulazioni avanzate, prevengono collisioni e ottimizzano in automatico le strategie di lavorazione per migliorare il rapporto tra velocità, qualità e durata dell’utensile.
- Materiali innovativi: lo sviluppo di superleghe, leghe di titanio sempre più performanti e materiali compositi pone nuove sfide alla fresatura CNC, stimolando la ricerca in utensili e processi di asportazione sempre più efficaci.
Conclusioni
La fresatura CNC rappresenta un pilastro portante nella lavorazione dei metalli per la sua capacità di coniugare precisione, efficienza e flessibilità. Dalla progettazione CAD/CAM all’ottenimento del pezzo finito, ogni fase richiede competenze specifiche e un approccio metodico, ma i benefici in termini di qualità del prodotto e riduzione dei costi di produzione sono notevoli.
L’adozione di buone pratiche, come la manutenzione preventiva e l’ottimizzazione dei parametri di taglio, garantisce risultati costanti e riduce il rischio di difetti. La scelta del materiale e dell’utensile più adatto, così come l’impiego corretto di sistemi di raffreddamento e di controllo in-process, concorrono ulteriormente a mantenere standard elevati di lavorazione.
Con l’avanzare di tecnologie legate all’industria 4.0, alla robotica e ai nuovi software di simulazione e programmazione, la fresatura CNC continuerà a evolvere, offrendo soluzioni ancora più intelligenti e integrate. In quest’ottica, investire in formazione e aggiornamento costante rappresenta la chiave per restare competitivi sul mercato e per sfruttare appieno il potenziale di questa tecnologia straordinaria.